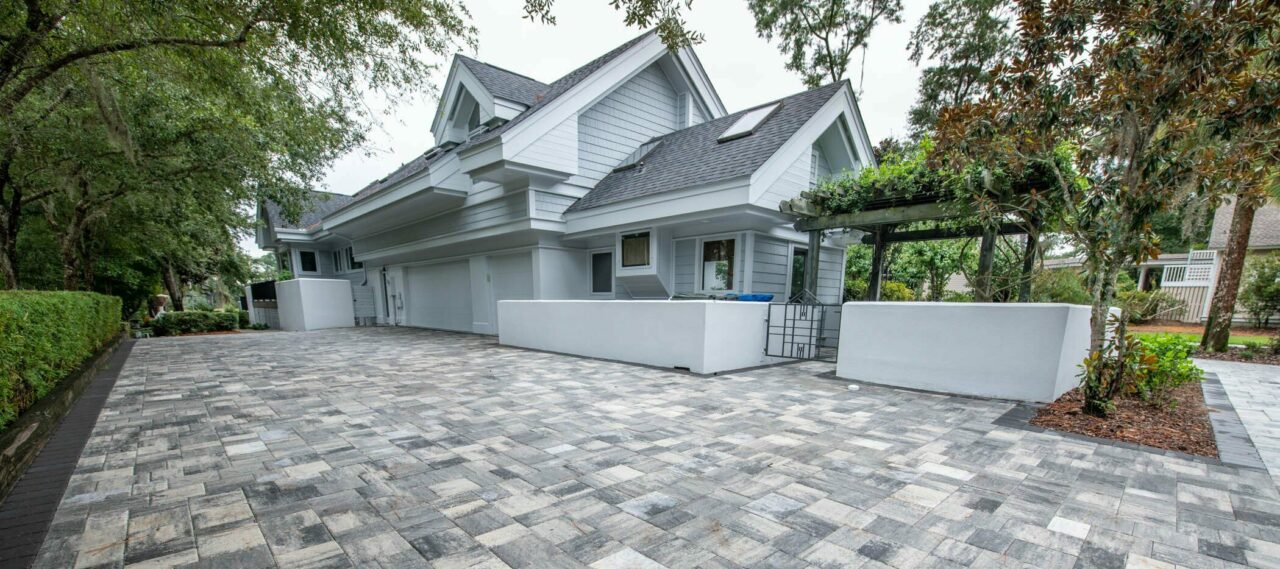
Paving a driveway is a common home improvement project that can enhance the curb appeal and functionality of your property. The cost of paving a driveway can vary significantly depending on various factors, including the type of material you choose, the size and condition of the driveway, labor costs, and your location.
In this detailed explanation, we will explore these factors and provide you with a comprehensive understanding of the costs involved in paving a driveway.
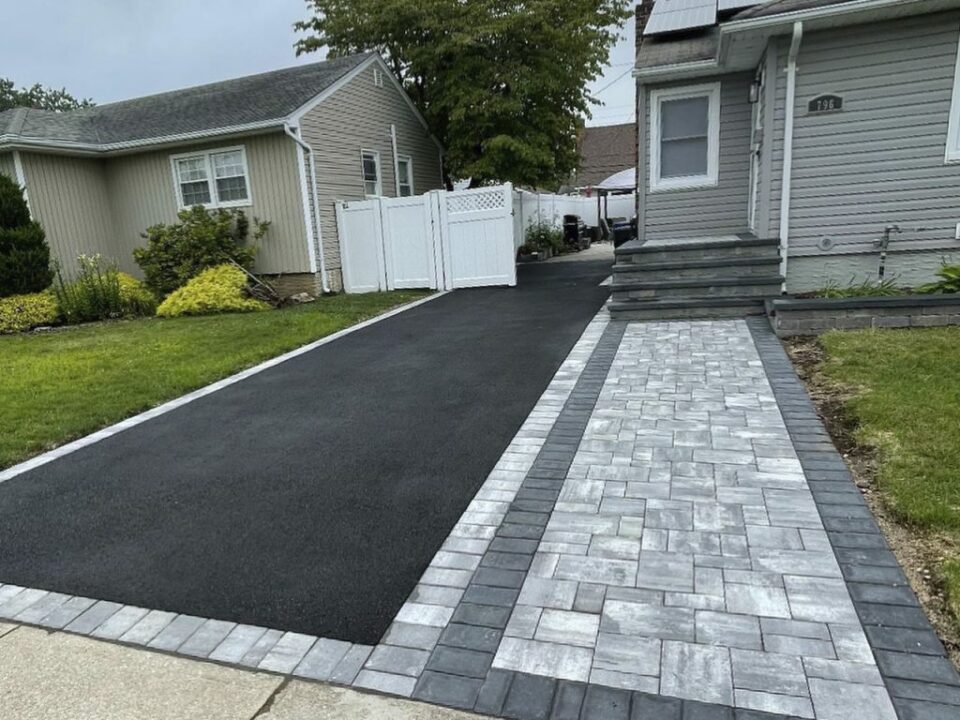
1. Material Selection:
The type of material you choose for your driveway is one of the most significant factors that will influence the cost. Here are some of the most common driveway paving materials and their respective costs:
a. Asphalt: Asphalt driveways are cost-effective and relatively easy to install. On average, you can expect to pay around $3 to $5 per square foot for a basic asphalt driveway installation. Keep in mind that the price may vary depending on your location and the quality of the asphalt used.
- Crude Oil Prices: Asphalt is derived from crude oil, so changes in global oil prices can directly impact the cost of asphalt. Higher oil prices typically lead to higher asphalt prices.
- Quality and Grade: Different grades of asphalt are available, and higher-quality asphalt often comes at a higher price. Contractors may recommend specific grades based on your location and intended use.
- Availability: Asphalt prices can vary regionally, depending on local suppliers and the proximity to asphalt refineries. More remote areas might experience higher material costs due to transportation expenses.
On average, asphalt costs typically range from $100 to $200 per ton. The quantity of asphalt required for your project depends on the size and thickness of the paved area.
b. Concrete: Concrete driveways are known for their durability and can last for decades. However, they are typically more expensive to install compared to asphalt. The cost for a concrete driveway can range from $4 to $10 per square foot, depending on the decorative finishes and design.
c. Gravel: Gravel driveways are the most affordable option, with costs ranging from $1 to $3 per square foot. They are easy to install but may require periodic maintenance and regrading to keep them in good condition.
d. Pavers: Paver driveways offer a high-end, customizable look. They come in various shapes, sizes, and colors, which can significantly impact the cost. Paver driveways can range from $8 to $20 per square foot, depending on the type of pavers and the complexity of the design.
2. Driveway Size:
Driveway size is a critical factor to consider when planning any paving project, be it for residential or commercial purposes. The dimensions of your driveway not only impact the aesthetics and functionality of your property but also play a significant role in determining the cost of the project. Let’s delve into the various aspects of driveway size and its importance in the context of paving:
a. Estimating the Square Footage: Driveway size is typically measured in square footage or square meters, depending on your region’s unit of measurement. The square footage of your driveway is calculated by multiplying its length by its width. For irregularly shaped driveways, multiple measurements may be needed to get an accurate estimate.
b. Impact on Paving Costs: The most direct influence of driveway size is on the overall cost of the paving project. Asphalt, concrete, or other paving materials are typically priced per square foot or square meter. A larger driveway will require more material, which increases material costs proportionally. Labor costs may also be higher for larger driveways, as they require more time and effort to prepare and pave.
c. Material Requirements: Different paving materials have specific thickness requirements to ensure durability and longevity. Larger driveways will require more material to meet the desired thickness. For example, if your project requires a 2-inch (5 cm) thick layer of asphalt, a 1,000-square-foot driveway will need more asphalt than a 500-square-foot driveway.
d. Design and Aesthetics: The size of your driveway can greatly impact the design and aesthetics of your property. A well-proportioned driveway can enhance the overall look of your home or business. Larger driveways offer more flexibility for decorative features, like borders, patterns, or landscaping elements.
e. Functionality and Space Utilization: The size of your driveway should align with its intended use. A larger driveway can accommodate more vehicles and provide space for turning and parking. This is especially important for commercial properties, where customers or employees require ample parking space. On the other hand, a smaller, more compact driveway may be more appropriate for residential properties with limited space.
f. Local Regulations: Local zoning regulations and homeowner association rules often stipulate the minimum and maximum allowable driveway sizes. These regulations are in place to ensure that driveways are proportionate to the property and do not encroach on public spaces or neighboring properties. Before planning your driveway, it’s essential to check local guidelines and obtain any necessary permits.
g. Maintenance and Durability: The size of your driveway can also impact long-term maintenance costs. A larger driveway may require more extensive sealing, resurfacing, or repairs over time, increasing maintenance expenses. Proper drainage planning is essential for larger driveways to prevent water-related issues.
h. Site Conditions: Consider the topography and features of your property when determining the size of your driveway. A hilly or sloped terrain may require a longer or wider driveway to ensure safe and convenient access. These factors can also affect excavation and grading costs.
i. Future Expansion: It’s a good practice to consider potential future needs when determining driveway size. If you anticipate changes in your household or business, like additional vehicles or increased traffic, it may be cost-effective to plan for a larger driveway from the outset.
In summary, driveway size is a fundamental aspect of any paving project, impacting costs, functionality, aesthetics, and compliance with local regulations. When planning your driveway, it’s essential to strike a balance between your budget, space requirements, and the desired look of your property. Consulting with a professional contractor can help you make informed decisions about driveway size, ensuring that it meets your needs and adds value to your property.
3. Site Preparation:
Proper site preparation is crucial to ensure a long-lasting and durable driveway. This includes clearing the area of any debris, grading the land for proper drainage, and compacting the soil or base material. Site preparation can account for a significant portion of the total cost, depending on the condition of your existing driveway or land.
Read also
- How to Clean Paving Stones – Easy Steps
- 9 Best Waterproof Patio Cover Ideas for Ultimate Outdoor Protection
- How to Lay Paving Slabs on a Slope – Easy Step by Step
4. Labor Costs:
Labor costs for driveway installation can vary based on your location and the complexity of the project. Labor costs typically include excavation, grading, laying the base material, and the actual paving. Skilled laborers may charge more for intricate designs or when working with specific materials like pavers.
Labor costs are a significant component of the overall expenses when it comes to paving, whether it’s a driveway, parking lot, or road. Labor costs encompass a range of tasks, and they can vary depending on factors such as location, the experience of the paving crew, the size and complexity of the project, and local wage rates. In this detailed explanation, we’ll break down the labor costs associated with paving:
a. Site Preparation:
- Clearing and Grading: Before the actual paving can begin, the area needs to be prepared. This involves clearing the site of debris, vegetation, and any existing materials, such as an old asphalt or concrete surface. Grading is also crucial to ensure proper drainage and a level surface. Labor costs for site preparation are determined by the extent of work required.
b. Paving:
- Asphalt or Concrete Application: The core of the labor cost is the application of the paving material, whether it’s asphalt or concrete. This process involves spreading, leveling, and compacting the material to achieve the desired thickness and a smooth, even surface. This is a critical step in the process and often requires a skilled crew to ensure a high-quality result.
- Complex Designs and Patterns: Some projects may require intricate designs or patterns, such as herringbone or decorative stamping for concrete. These designs demand more labor and expertise, which can add to the overall cost.
c. Compaction and Finishing:
- Compaction: Once the paving material is in place, it must be compacted to achieve the required density. Compaction ensures that the material settles properly and forms a stable, long-lasting surface.
- Finishing: Proper finishing is essential for a smooth and aesthetically pleasing surface. This includes smoothing out any imperfections, edges, or joints. The final appearance of the pavement often depends on the skill of the finishing crew.
d. Edging and Sealing:
- Edging: Some projects may include the installation of decorative or functional edging to enhance the aesthetics or structure of the paved area. Labor costs for edging vary depending on the type of material and design.
- Sealing: After the initial paving is complete, some projects may require sealing to protect the surface and extend its lifespan. The application of sealant also involves labor costs.
e. Crew Size and Skill:
The number of workers needed for a paving project can vary. Smaller residential projects like driveways may require a small crew, while larger commercial or road projects often involve multiple workers and specialized equipment. The skill and experience of the crew members can also influence labor costs. Highly skilled workers may charge higher hourly rates but can ensure a higher-quality result.
f. Hourly Rates:
Labor costs are typically calculated on an hourly basis. The hourly rates for laborers can vary widely across different regions of the United States, influenced by local economic conditions, demand for labor, and prevailing wage rates. Hourly rates for paving laborers typically ranged from $50 to $100 per hour per worker. Skilled laborers, such as those operating heavy machinery, might command higher rates.
g. Project Duration:
The time it takes to complete a paving project affects labor costs. Larger projects or those with more intricate designs will require more time and, therefore, higher labor costs. Some projects may be completed in a day, while others could span several weeks.
h. Safety and Compliance:
Labor costs also include adherence to safety regulations and best practices. Paving crews must follow safety guidelines to protect themselves and ensure a safe working environment. This might involve additional training and safety equipment, which can impact costs.
i. Unforeseen Circumstances:
Sometimes, unexpected issues may arise during the project, such as adverse weather conditions or the need for adjustments due to unforeseen obstacles. Dealing with these challenges may require additional labor hours, affecting costs.
In conclusion, labor costs for paving are a crucial part of any paving project’s budget. They encompass various tasks, from site preparation to the actual paving and finishing. The specific labor costs for a project will depend on factors like project size, complexity, location, and the skill level of the crew.
It’s important to obtain detailed estimates from contractors, considering both material and labor costs, to accurately budget for your paving project. Hiring an experienced and reputable contractor can ensure that the labor component of your project is executed efficiently and effectively, resulting in a high-quality pavement surface.
5. Additional Costs:
Several other factors can contribute to the overall cost of driveway paving:
a. Drainage: Proper drainage is essential to prevent water from pooling on your driveway. Depending on the slope of your property and local regulations, you may need to install drainage systems, which can add to the cost.
b. Edging and Borders: Adding decorative edging or borders can enhance the aesthetics of your driveway but will increase the overall cost.
c. Sealcoating and Maintenance: While not part of the initial installation cost, it’s essential to budget for ongoing maintenance, such as sealcoating for asphalt driveways or resealing for concrete driveways, to extend their lifespan.
d. Permits and Regulations: Be sure to check if your local municipality requires permits for driveway installation, as this may involve additional costs.
6. Location and Regional Variations:
The cost of driveway paving can vary significantly based on your location. Urban areas tend to have higher labor and material costs, while rural areas may offer more competitive rates. Climate and weather conditions in your region can also affect the type of material recommended and the cost of installation.
Read more:
- 95 Best Backyard Remodel Ideas – Wood & Concrete Accent
- 43 Best Cozy & Beautiful Backyard Pool Ideas
- Backyard Living Inspiring Ideas to Level up Your Space
7. Contractor Selection:
The choice of a contractor can impact the overall cost. Experienced and reputable contractors may charge higher rates for their services, but they can provide quality workmanship and ensure the project is completed on time and within budget. It’s essential to obtain multiple quotes from different contractors and carefully review their credentials and past projects.
8. DIY vs. Professional Installation:
Some homeowners may choose to tackle driveway paving as a do-it-yourself project to save money. While this can reduce labor costs, it’s important to remember that proper installation requires skill and equipment. Mistakes can lead to costly repairs in the long run. Hiring a professional is often the safest and most efficient way to get the job done.
9. Cost Estimation Example:
Let’s consider an example to estimate the cost of a driveway installation. Suppose you want to pave a 500 square foot driveway using asphalt in a suburban area.
- Material cost (asphalt): $3 to $5 per square foot
- Labor cost: $2 to $4 per square foot
- Site preparation: $1,000 to $2,000
- Total cost estimate: (500 sq. ft. x $3) + (500 sq. ft. x $2) + $1,000 = $2,500 (low end) to (500 sq. ft. x $5) + (500 sq. ft. x $4) + $2,000 = $6,500 (high end)
This is a basic estimate, and the actual cost may vary depending on the factors mentioned earlier.
In conclusion,
the cost of paving a driveway can range from a few thousand dollars to tens of thousands of dollars, depending on the materials chosen, the size of the driveway, labor costs, and various other factors. It’s essential to obtain multiple quotes from contractors, consider your budget, and assess the long-term maintenance requirements when making your decision. Investing in a well-constructed driveway can not only enhance the aesthetics of your property but also add value and convenience to your daily life.